How to Choose Between a Drop-Through vs. Blow-Through Rotary Valve
When selecting a rotary valve for your pneumatic conveying systems, there are many design options to consider such as size, materials of construction, and compliance to industry standards. Among these choices, one important factor that stands out is configuration.
When selecting a rotary valve to feed a pneumatic conveying line there are generally two types of configurations: drop-through and blow-through, sometimes called “blowing seal.” But how do you determine which one is best suited to feed your product through your pneumatic conveyor?
Read on to learn more about why choosing the right configuration is important, as well as the differences, benefits, and applications of each type.
Why Choosing the Right Rotary Valve Configuration is Important
To put it simply, valve configuration has a significant impact on how well powder moves through your pneumatic conveying system. As you know, powder type, texture, and size are important factors to consider.
Rotary valves not only control powder flow, they can also act as a safety mechanism. If the powder has combustible properties, the right rotary valve will act as a flame barrier and process isolator in case of an explosion.
Let’s walk through the differences, benefits, and applications of each rotary valve configuration.
Differences Between Blow-Through and Drop-Through Rotary Valves
Drop-through rotary valves are the most basic and common type of rotary valve. They feed material that falls through the inlet, moves down though the rotating vanes where it drops out the bottom outlet flange via gravity. This design is capable of feeding materials in a vast array of applications. In a pneumatic conveying system, a convey adapter or shoe must be installed below the valve to transfer the product into the conveying line where it is blown or sucked downstream.

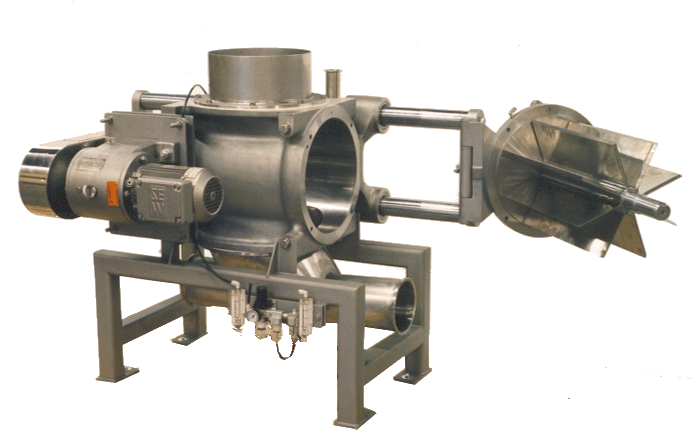
On the other hand, blow-through rotary valves don’t have an outlet flange on the bottom side like a drop-through. The bottom of the housing bore is either smooth or has a trough, which is where the pneumatic conveying line connects and runs through the bottom of the valve. Material feeds into the inlet like a drop-through, but as the rotor passes material to the underside of the valve it’s “blown” directly out of the rotor pockets into the conveying line downstream.



Applications & Benefits of Drop-Through Rotary Valves
The drop-through valve is used mainly for relatively free-flowing, non-cohesive materials such as grain, rice, coffee beans, salt, and sugar.
With a properly designed adapter feeding material from the valve outlet into the convey line, air leakage across the rotary valve can be reduced in high pressure pneumatic conveyors. This decreases the effects of upward airflow restricting material feed into the valve inlet.
A drop-through design may be your best option when there are a number of rotary valves in series on a single convey line. In this circumstance, a blow-through design could put too much resistance on the product and cause it to break down, while the obstruction-free convey transition under a drop-through design may better protect the product’s integrity.
Another benefit of drop-through rotary valves is in applications were cleaning the interior of the valve is essential for product safety. With a drop-through design the internal area of the rotary valve can be accessed without dismantling convey line connections. This makes cleaning quicker and easier.
Applications & Benefits of Blow-Through Rotary Valves
Blow-through valves are ideal for more cohesive or sticky powders like cocoa, flour, or milk powders. These powders may not discharge properly from a drop-through rotary valve, compacting and sticking to the inside of the rotor vanes. In a blow-through rotary valve, discharge is optimized by blowing these easily compacted powders out of the rotor pockets, which helps keep the rotor clear of buildup.
Another advantage of blow-through rotary valves is their low profile. Compared to a drop-through valve of similar size, the blow-through systems’ conveying line runs much closer to the valve centerline allowing it to take up much less height. This makes blow-through rotary valves a good choice for low-clearance installations where a drop-through may not fit.